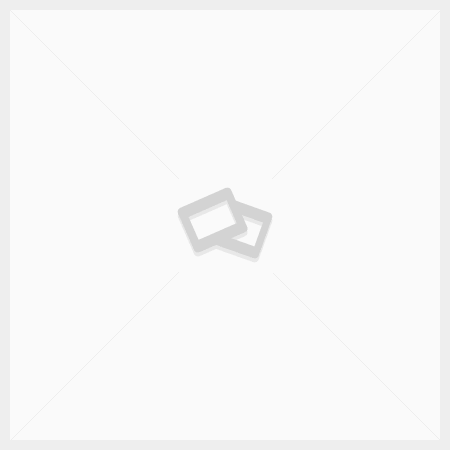
Effective Ways to manufacture Right-Hand Straight Turning Tools
Raw materials Used:
1] Bright drawn steel rods of 16x16mm to AISI 1018 specification.
2] Carbide tips as per ISO A12 of suitable grade.
Procurement of Raw materials:
1] Procure steel rods from approved sources only along with material test certificates.
2] Procure carbide tips from the approved source in Europe or from Kennametal in India. Tectools Engineering a manufacturer of Cutting Tools & Threading Tools, Carbide Tools & Lathe Tools procures the best carbide tips from Europe and India.
Inspection of Raw materials:
1] Carry out chemical analysis of the steel rods and check against specifications
2] Visually inspect the steel rods for defects such as cracks, deep dents and heavy scoring marks and clear materials if ok on all the above matters for manufacture.
3] Check the grade of the carbide tip to ascertain that the right grade is being used for manufacture of the tools.
Right Hand Straight Turning Tools Manufacturing Procedure:
1] Set and cut steel rods to lengths of 113+ 3 mm and check.
2] Set and Mill the front approach and clearance angle of the turning tools at 20 deg x8 deg to maintain C dimension at 7 to 8 mm and check.
3] Set and mill the side approach and clearance angle of the turning tools at 20 deg x8 deg to maintain C at 6.2 to 5.8 mm and check.
4] Set and mill the top rake face at 90 deg to the side approach angle and generate a positive rake of 11 deg and check
5] Set and mill the tip pocket of the cutting tools & threading tools parallel to the top rake face to ensure that the carbide tip protrudes outside the steel shank by at least 0.8 mm, maintain height over carbide tips between 15.8 and 16.2 mm and C dimension at 5.8 to 6.2. Check.
6] De burr the shanks of the cutting tools and stamp the designation as DIN 4971 / ISO 1 R 1616 P30 and check.
7] Carryout inspection of all operations done so far.
8] Grind the carbide tips to remove the sintered surfaces on the brazing area.
9] Degrease the shanks of the turning tools and the carbide tips and ensure that the brazing area is free of rust.
10] Procure Silver foil of 0.1 mm thickness having min of 49% silver content and devoid of any Tin or Lead from Degussa in Germany or from an approved source in India
11] Apply suitable brazing flux on the tip seat area, build up a sandwich of 2 silver foils and a copper foil in between with brazing flux in between them and place them on the tip seat area, apply brazing flux to the area of the tip that gets brazed, place the tip to be brazed on top of the sandwich of foils. Allow to dry.
11] Set the Induction brazing machine with a suitable induction coil and power tapping points.
12] Insert the turning tool to be brazed with the carbide tip into the induction coil and start heating. Stabilise heating when the steel shank turns from blue to mild red in colour. Start heating again to take the carbide tip and the steel area surrounding it to the melting point of silver. Press the tip into position with a pointer rod and allow the turning tools to cool to about 200 deg C. Remove the tool from inside the induction coil and place it in pre heated sand and allow it to cool to the room temperature.
13] Inspect the joint to ensure that the carbide tip is brazed properly onto the shank and that the silver has flown properly and that there are no gaps in the joint.
14] Set and grind the top rake angle, front clearance angle, side clearance angle and corner radius of 0.4mm on the carbide tips as per drawing and check.
15] Carry out final inspection of the cutting tools for dimensions and defects on carbide tips prior to painting.
16] Apply a cloth tape on the tips or hot dip the carbide tips in a plastic medium and wash the tools in a chemical that cleans, degreases and phosphates the shank prior to painting.
17] Paint the tools and apply colour code at the back end to identify the grade.
Dark Blue for P20, light blue for P30, Red for K20 and Yellow for M20.
18] Pack the turning tools in a suitable corrugated box and ship out.